Understanding Corrosion
- social3204
- Apr 17, 2023
- 5 min read
Updated: May 20

INTRODUCTION
Corrosion is a pervasive and costly phenomenon that affects various materials, especially metals and alloys, leading to their deterioration over time. This technical bulletin aims to provide a concise overview of corrosion, including its definition, causes, types, and prevention methods.
DEFINITION
Corrosion is a natural electrochemical process that occurs when a material interacts with its environment, resulting in the gradual degradation and loss of its original properties. It involves the oxidation of metals, often accelerated by the presence of moisture, oxygen, and other corrosive substances.
Several factors contribute to the occurrence of corrosion:
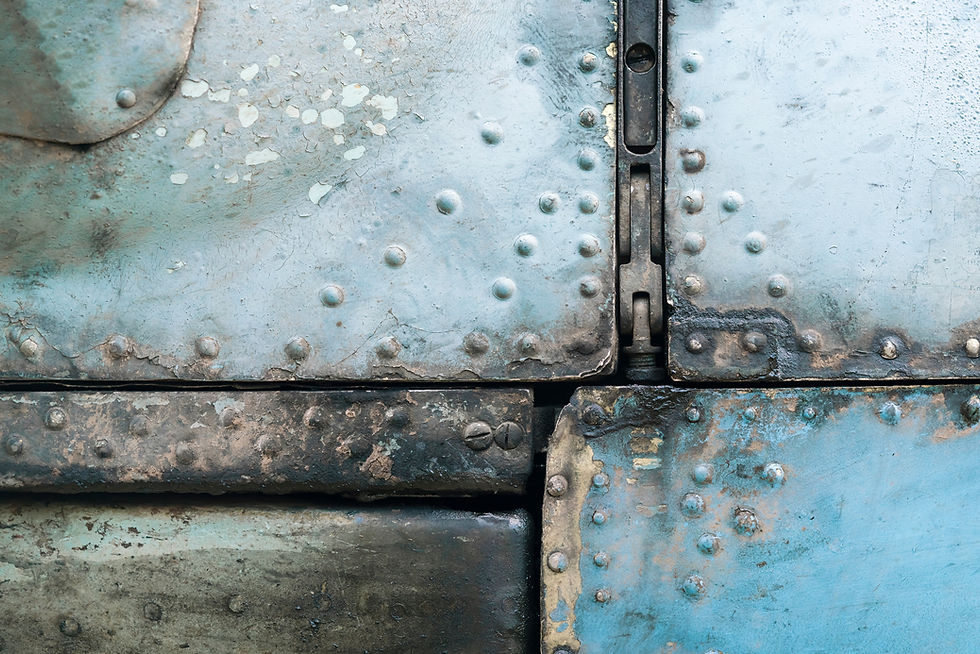
Electrochemical Reactions: Corrosion is primarily an electrochemical process involving the transfer of electrons between metal atoms and the surrounding environment. The formation of anodes and cathodes on a metal surface accelerates the corrosion process.
Moisture: The presence of moisture, such as humidity, water, or moisture-laden air, plays a crucial role in facilitating corrosion. It provides the necessary medium for ionic conduction and promotes the oxidation reactions required for corrosion.
Oxygen: Oxygen is a key contributor to corrosion, as it supports the oxidation reactions that lead to the breakdown of metals. The presence of dissolved oxygen in aqueous environments significantly accelerates the corrosion rate.
Chemical Agents: Corrosion can be accelerated by exposure to various chemicals, including acids, alkalis, salts, pollutants, and aggressive gases. These substances can initiate or enhance corrosion processes, often by altering the electrochemical environment.
TYPES OF CORROSION
Corrosion can manifest in different forms, depending on the specific conditions and mechanisms involved. Some common types of corrosion include:
Uniform Corrosion: Uniform corrosion, also known as general corrosion, is the most common form of corrosion. It occurs when the entire surface of a metal is corroded at a relatively uniform rate. The metal gradually loses material thickness, resulting in a reduction of structural integrity. Uniform corrosion is typically influenced by factors such as exposure to moisture, oxygen, and corrosive substances in the environment. It often manifests as a gradual thinning or etching of the metal surface.
Pitting Corrosion: Pitting corrosion is characterized by the localized formation of small cavities or pits on the metal surface. It occurs when a localized breakdown of the protective oxide layer exposes the underlying metal to corrosive agents. Pitting corrosion can be particularly detrimental as it can penetrate deeply into the metal, leading to severe structural damage even with minimal visible signs on the surface. It is commonly found in environments with high chloride concentrations, such as coastal areas or industrial settings where corrosive chemicals are present.
Galvanic Corrosion: Galvanic corrosion, also known as bimetallic corrosion, occurs when two dissimilar metals or alloys come into contact in the presence of an electrolyte. The metals form a galvanic cell, where one metal acts as the anode and corrodes while the other metal acts as the cathode and remains protected. The extent of corrosion depends on the difference in electrochemical potentials between the two metals. Galvanic corrosion is often observed in applications involving dissimilar metals, such as plumbing systems or the use of different metals in marine environments.
Crevice Corrosion: Crevice corrosion occurs in confined spaces or crevices, such as gaps, joints, or under deposits, where stagnant conditions exist. These areas restrict the flow of oxygen and prevent the removal of corrosive substances, creating localized corrosive environments. Crevice corrosion can be exacerbated by factors such as moisture entrapment, differential aeration, and the accumulation of debris or deposits. It is commonly found in crevices between two metal surfaces, under gaskets, in bolted connections, or in areas where coatings have been damaged.
Stress Corrosion Cracking (SCC): Stress corrosion cracking is a specific type of corrosion that occurs when a metal is subjected to a combination of tensile stress and a corrosive environment. The presence of both factors leads to crack initiation and propagation, even under relatively low applied stress levels. SCC can be highly dangerous as cracks can propagate rapidly and cause catastrophic failures without significant visible deformation or signs of corrosion on the surface. This type of corrosion often affects materials in industries such as oil and gas, chemical processing, and aerospace.
Intergranular Corrosion: Intergranular corrosion occurs along the grain boundaries of a metal, typically due to the segregation of impurities or alloying elements along these boundaries. This type of corrosion can result in selective depletion of certain elements along the grain boundaries, making them more susceptible to corrosion. Intergranular corrosion can lead to structural weakness and failure, especially in materials with poor grain boundary corrosion resistance. It is often observed in alloys such as stainless steel, aluminum alloys, and certain nickel-based alloys.
CORROSION PREVENTION AND CONTROL
Various strategies can be employed to prevent or minimize corrosion:
Protective Coatings: Protective coatings are widely used to create a barrier between the metal surface and the corrosive environment. These coatings can be in the form of paints, polymers, metal platings, or conversion coatings. They act as a physical barrier, preventing direct contact between the metal and corrosive agents. Additionally, some coatings provide sacrificial protection by releasing corrosion-inhibiting compounds or acting as a reservoir for corrosion products. The selection of the appropriate coating depends on factors such as the type of metal, the corrosive environment, and the desired lifespan of the protection.
Cathodic Protection: Cathodic protection is an electrochemical technique used to control corrosion by making the metal surface the cathode of an electrochemical cell. There are two primary types of cathodic protection:Sacrificial Anode Cathodic Protection: In this method, a more reactive metal (sacrificial anode) is connected to the metal to be protected. The sacrificial anode corrodes preferentially, while the metal to be protected remains cathodic and is shielded from corrosion. Common sacrificial anode materials include zinc, aluminum, and magnesium.
Impressed Current Cathodic Protection: In this method, an external power source is used to supply a controlled direct current to the metal surface, making it cathodic. This technique is often employed when the structure to be protected is large or when sacrificial anodes are impractical. Impressed current cathodic protection is commonly used in pipelines, offshore structures, and reinforced concrete.
Material Selection: Choosing corrosion-resistant materials is an effective strategy for preventing corrosion in specific applications. Different metals and alloys exhibit varying degrees of corrosion resistance in different environments. Stainless steel, aluminum, titanium, and corrosion-resistant alloys, such as Hastelloy and Inconel, are commonly used in industries where corrosion resistance is critical. Proper material selection based on the anticipated environment and corrosive agents can significantly reduce the likelihood of corrosion.
Environmental Control: Modifying the environmental conditions can help mitigate corrosion effects. Some approaches include:Moisture Control: Minimizing or eliminating moisture contact by keeping structures dry, applying waterproof coatings, or implementing effective drainage systems can help reduce the risk of corrosion.
Temperature and Humidity Control: Controlling temperature and humidity levels can mitigate corrosion, especially in environments where condensation or high humidity is a concern. This can be achieved through ventilation, insulation, or air conditioning systems.
pH Control: Maintaining the appropriate pH level in aqueous environments can help mitigate corrosion. For example, in closed cooling systems, proper water treatment with corrosion inhibitors can be employed to control pH and reduce corrosion rates.
Contaminant Control: Preventing or removing contaminants, such as salts, acids, or pollutants, from the environment can minimize corrosion. This can be achieved through filtration, proper waste management, or the use of protective barriers.
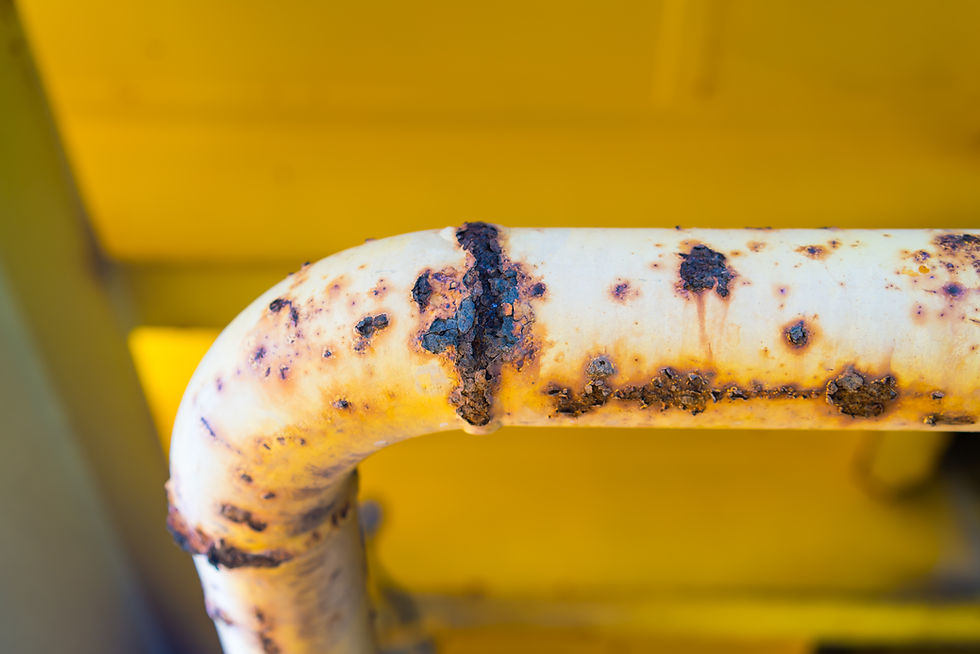
Implementing effective corrosion prevention and control strategies is essential for ensuring the longevity, safety, and reliability of structures, equipment, and components. It is important to consider the specific requirements of each application and seek guidance from corrosion specialists or materials engineers to select and implement the most appropriate corrosion prevention measures.
Corrosion is a complex phenomenon that can cause significant damage and financial losses in various industries. Understanding the causes, types, and prevention methods associated with corrosion is crucial for developing effective strategies to combat this persistent problem. By employing appropriate corrosion prevention techniques, industries can extend the lifespan and integrity of materials, ensuring safer and more durable structures and products.