Understanding Coatings
- social3204
- Apr 17, 2023
- 2 min read
Updated: May 20
INTRODUCTION
Coatings play a pivotal role in various industries, offering protection, functionality, and aesthetic appeal to a wide range of surfaces and substrates. This technical bulletin provides a comprehensive overview of coatings, including their definition, types, application methods, and key considerations.
DEFINITION AND PURPOSE
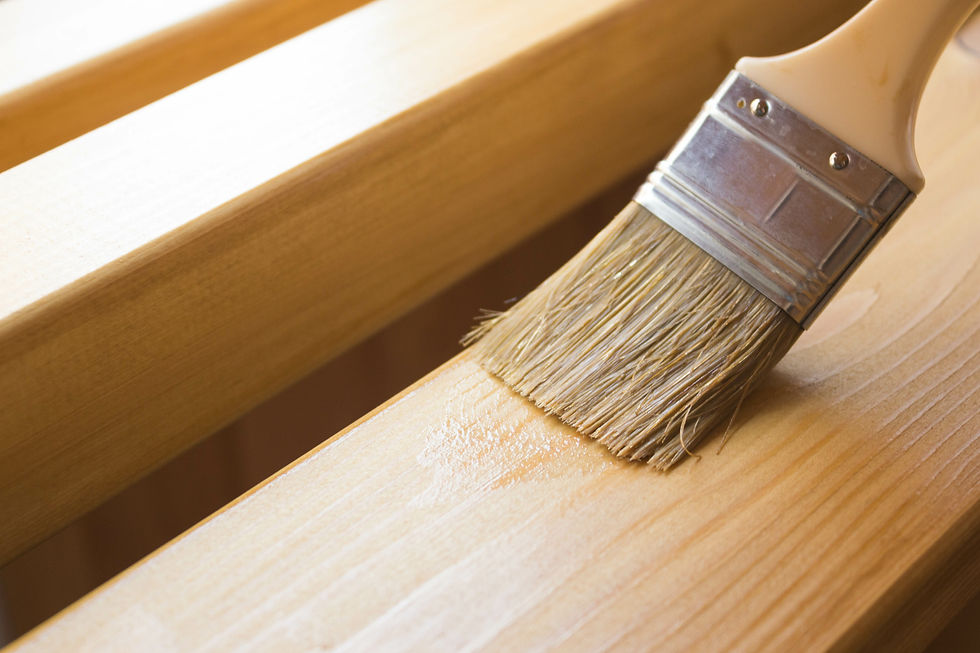
A coating is a material applied to a surface or substrate to enhance its properties and provide a protective layer. The purpose of a coating can vary, but it generally includes one or more of the following objectives:
Protection: Coatings shield substrates from environmental factors such as corrosion, UV radiation, abrasion, and chemical exposure.
Decoration: Coatings enhance the visual appearance of surfaces by providing color, gloss, texture, or other decorative effects.
Functionality: Coatings can add specific functionalities like anti-static, anti-reflective, self-cleaning, or anti-fouling properties to the coated surface.
TYPES OF COATINGS
Coatings are available in a wide range of types, each designed to fulfill specific requirements. Some commonly used coatings include:
Paints: Paint coatings provide decorative and protective properties, typically consisting of pigments, binders, and solvents. They are commonly used on metal, wood, and plastic surfaces.
Powder Coatings: These coatings are applied as dry powder and cured under heat, forming a durable, uniform layer. Powder coatings are known for their excellent adhesion, resistance to impact, and wide color range.
Polymer Coatings: Polymer-based coatings, such as epoxy, polyurethane, and acrylic coatings, offer exceptional chemical resistance, durability, and adhesion. They find applications in industries like automotive, aerospace, and construction.
Ceramic Coatings: Ceramic coatings provide high-temperature resistance, excellent hardness, and thermal insulation properties. They are commonly used in applications involving extreme temperatures, such as automotive exhaust systems and turbine engines.
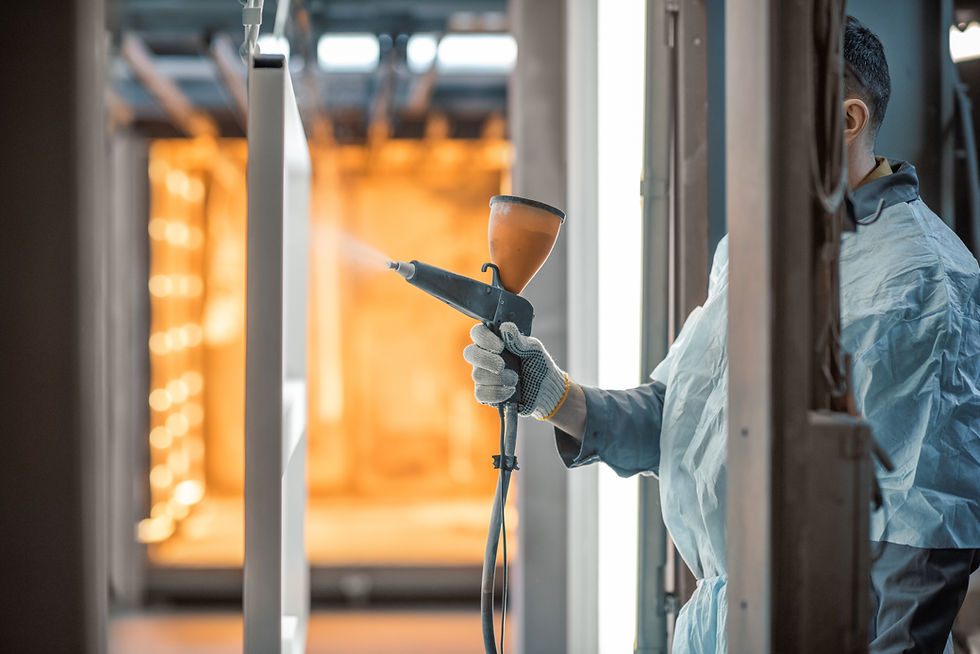
APPLICATION METHODS
Coatings can be applied using various methods, depending on the type of coating and the intended surface. The most common application methods include:
Spraying: Coatings can be sprayed onto surfaces using air or airless spray guns, providing a uniform and controlled layer thickness.
Brushing/Rolling: This manual application method involves using brushes or rollers to apply coatings on flat or contoured surfaces.
Dipping: Immersing the substrate into a coating bath allows for complete coverage of complex shapes and small parts.
Electrostatic Deposition: In this method, the coating is electrostatically charged, attracting it to the grounded substrate, resulting in uniform and high-quality coating.

KEY CONSIDERATIONS
When selecting a coating, several factors should be considered:
Substrate Compatibility: The coating must be compatible with the substrate material to ensure proper adhesion and long-term performance.
Environmental Conditions: The coating should be chosen to withstand the specific environmental conditions, such as temperature variations, humidity, UV exposure, and chemical exposure.
Application and Curing Process: Understanding the application method and curing process required for the coating is essential to ensure proper adhesion and optimal performance.
Maintenance and Durability: Coatings should be evaluated for their durability, ease of maintenance, and potential for repair or recoating.